Ensuring Safety And Security and Precision in Pipe Welding Inspection
In the realm of pipe welding evaluation, making sure security and precision are vital purposes that demand thorough attention. The stability of pipes rests on the top quality of welds, making the evaluation procedure an important facet of maintenance and building. As pipes traverse huge ranges carrying vital sources, any compromise in welding top quality could have significant effects. In light of this, the discussion bordering precaution and accuracy in inspection methods comes to be not only an issue of protocol but a foundational component in upholding the reliability and durability of our crucial infrastructure.
Significance of Pipeline Welding Evaluation
Pipe welding assessment is important for guaranteeing the integrity and safety of the framework. Through thorough evaluation, prospective issues, such as fractures, insufficient penetration, or imbalances, can be discovered and rectified prior to they lead to devastating failings.
Appropriate examination methods, such as aesthetic testing, radiographic screening, ultrasonic testing, and magnetic fragment testing, are used to evaluate the top quality of welds. These methods aid make sure that welds fulfill market criteria and regulative needs. By identifying and addressing flaws early in the welding procedure, the danger of leakages, tears, and ecological contamination is significantly minimized.
In addition, pipeline welding evaluation plays a vital role in maintaining conformity with safety and security requirements and policies. Regular examinations not just improve the structural honesty of pipes however likewise add to the overall safety and security of procedures and personnel operating in the location. Basically, investing in thorough pipe welding evaluation is a proactive action to avoid costly fixings, reduce risks, and promote the dependability of vital infrastructure.
Advanced Inspection Technologies
Advanced inspection modern technologies play an essential function in making certain the stability and security of pipe systems. One of the most noticeable innovations in pipe welding inspection is the use of automated ultrasonic testing (AUT)
Additionally, the application of phased variety ultrasonic screening (PAUT) has actually changed the examination procedure by giving detailed imaging of welds in real-time. PAUT offers better problem detection capabilities and enables for quick data analysis, enabling inspectors to make informed choices without delay - Pipeline Welding Inspection. In addition, electronic radiography (DR) has actually ended up being progressively preferred in pipe welding examination as a result of its ability to produce premium pictures that improve problem exposure while reducing radiation exposure
Incorporating these innovative assessment innovations not only boosts the high quality of weld assessments but also boosts general safety standards in pipe building and maintenance.
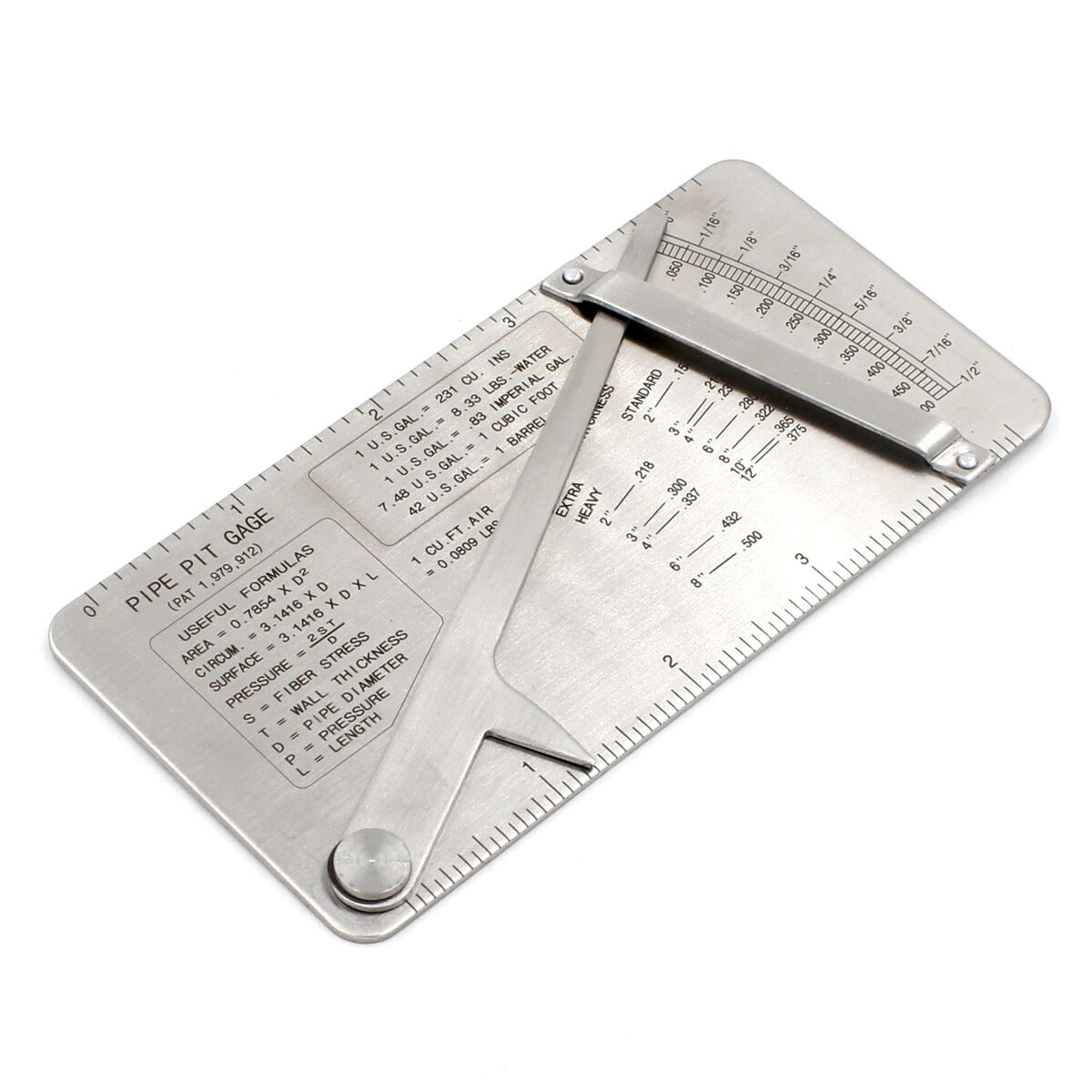
Function of Trained Inspection Professionals
The integration of innovative examination innovations in pipeline welding evaluation emphasizes the important significance of trained examination experts in guaranteeing the accuracy and integrity of evaluations. Educated assessment experts play a pivotal duty in supervising the execution of these innovations, interpreting the information obtained, and making educated choices based upon their experience.

These experts are outfitted with the required knowledge and abilities to conduct complete assessments, recognize possible problems or abnormalities in welds, and ensure conformity with market criteria and guidelines. Their ability to examine information, recognize patterns, and troubleshoot problems is essential in preserving the stability and safety and security of the pipeline facilities.
In addition, trained assessment specialists function as a vital web link in between technology and useful application. By leveraging their experience and training, they can give valuable insights, suggestions, and options to maximize the welding procedure and minimize risks efficiently.
Safety And Security Actions in Welding Evaluation
Effective execution of security steps in welding inspection is vital to guaranteeing the protection of employees and the stability of the infrastructure. Employees entailed in welding assessment must use appropriate individual protective tools (PPE) such as safety helmets, handwear covers, security glasses, and fire-resistant apparel to reduce the threat of injuries.
Routine safety and security training sessions must be conducted to enlighten evaluation specialists on the newest safety and security procedures and methods. It is critical to have emergency feedback plans in area to deal with any unanticipated incidents without delay. Inspectors must be watchful in checking the welding equipment frequently to recognize any prospective safety and security risks. By prioritizing safety and security measures in welding evaluation, companies can develop a protected functioning original site setting and maintain the top quality and reliability of pipe infrastructure.
Ensuring Precision in Evaluation Practices
With a concentrate on thorough attention to detail, accomplishing accuracy in examination practices is necessary for guaranteeing the high quality and integrity of pipe welding. Accuracy in assessment methods includes adhering to strict standards and guidelines to properly analyze the welds for any kind of flaws or flaws. Using advanced evaluation technologies such as ultrasonic testing, radiographic testing, and aesthetic evaluation methods is essential in determining even the smallest flaws that can endanger the safety and capability of the pipe.
Making certain accuracy in assessment practices also requires well-trained and competent inspectors who have a deep understanding of welding processes, products, and market policies. These assessors have to have the capability to interpret examination outcomes precisely and make notified decisions pertaining to the approval or being rejected of welds based upon predefined requirements.
Regular calibration and maintenance of inspection equipment are critical to assuring the dependability and precision of assessment outcomes. By supporting high requirements of precision in assessment techniques, over here stakeholders can believe in the structural stability and efficiency of pipeline welds, inevitably contributing to the overall security and effectiveness of the pipeline system.
Verdict
In conclusion, the significance of pipeline welding inspection can not be overstated. Advanced examination innovations and skilled inspection experts play an essential role in making certain safety and security and precision in welding techniques. By following stringent precaution and maintaining accuracy in assessment procedures, the honesty of pipes can be promoted, securing against prospective risks and making sure the continued performance of the system.
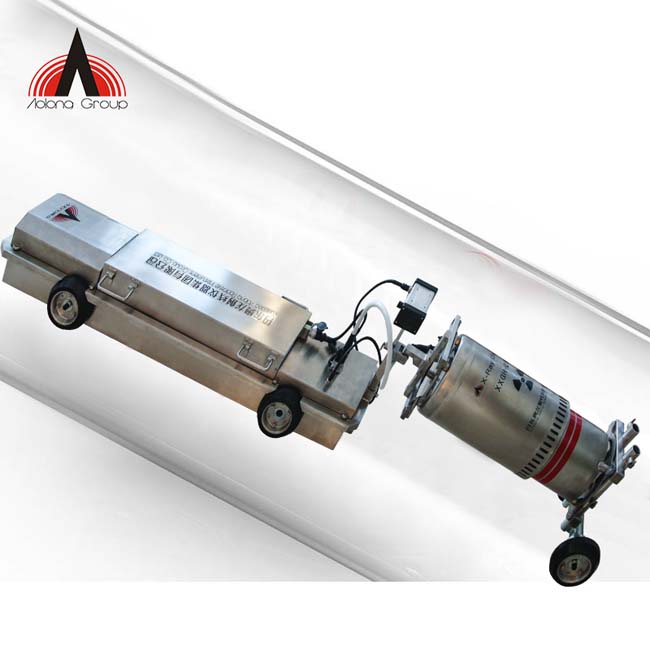
Making use of innovative evaluation innovations such as ultrasonic screening, radiographic screening, and visual inspection methods is crucial in determining also the smallest flaws that might compromise the security and capability of the pipe.
Advanced inspection modern technologies and qualified examination specialists play a vital role in ensuring safety and accuracy in welding techniques.
Comments on “Optimize Performance: Proactive Pipeline Welding Inspection Approaches”